Case Histories...
Project
Case Studies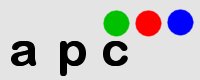
APC has successfully completed projects in many industries utilizing a large
number of different technologies. The following is a synopsis of the type of
work that we are capable of and confirms our solutions based approach.

Problem:
Loss of production due to manual loading of crusher system. Solution:
Design and build of advanced control system to automate the feed and operation
of hydraulic crusher. Consequently, production increased and the customer
realized a significant cost saving. Technology
Used: Allen Bradley PLC integrated into the existing control system
and communication to field devices over an Interbus bus system. 
Problem: Product quality
problems caused by poor operator monitoring and lack of data logging system. Solution:
To replace unreliable human eyes, an eight camera real time vision
system was designed and implemented by APC. The system incorporated PC based
control and logging of production. Thus, final product quality was greatly
improved and the image logs produced provide valuable manufacturing data. The
system is very versatile and the same technology has been successfully used in
many industries to replace visual quality checks carried out by human eyes. Technology
Used: CCD video cameras, PLC based controls, Siemens HMI and PC based
image recording. 
Problem:
Operator errors caused by incorrect part selection leading to poor productivity
and wastage of good parts. Solution:
Design and installation of automatic part identification system to ensure
correct part selection. The system features mechanical and electrical interlocks
to prevent the operator selecting and fitting the wrong part for the item in
production. A system of lamps indicates which part is to be selected, a sensor
on the part bin further ensures correct part selection. Thus correct part
selection is ensured and costly wastage eliminated. Technology
Used: PLC based controls, remote I/O, Serial interface into existing
controls. Problem:
Verification of product ageing performance to ensure correct life of the
finished product. Solution:
Design and installation of roofing panel accelerated ageing test rig with real
time vision system to monitor results. The project required a rapid turnaround
to meet production levels as well as power monitoring and control. Technology
Used: IR heat lamps with closed loop control and re-circulating water
cooling system. Siemens PLC and HMI. PC based camera monitors and data logging.
The system is fully automatic, no operator is required thus a large cost saving
was realised.  Do
you have a problem in your production process? We have the expertise to improve
your productivity. Contact us.
|